
Heavy-Lift Agricultural Drone
Lead
Aeropace
Engineer
Role
Industry
Aerospace
Drones
Duration
Tools
Fusion 360,
Aerofoil
~6 months
Aerospace Engineering
Aircraft Design
Propulsion
Skills
I joined Venture Aerospace as an early founding engineer (1 of 2), where I was responsible for developing the aerodynamic design of a jet-powered, heavy-lift, long-endurance agricultural drone. Equipped with advanced sensors for crop diagnosis and treatment, the drone aimed to enhance precision agriculture. In addition to creating detailed airfoil design blueprints, I also developed a centrifugal compressor design that was filed for preliminary patent.
Design of Long-Endurance, Heavy-Lift Drone
Due to the unforeseen financial impact of the COVID-19 pandemic, the project was cut short as the company—along with much of the aerospace industry—temporarily lost funding.
Design Process
1. RESEARCH |
We performed extensive research on the existing agricultural technology and drone markets. We found that, at that time, most drones were battery powered, meaning that they were limited to a runtime of ~90 minutes.
For agricultural crops that span hundreds of
acres and would likely take hours to inspect and treat, we needed a power solution that would be long endurance. Moreover, we needed a drone that had a high payload capacity, to carry agricultural material across crops. Thus, we looked to the best example there was for long endurance, high-payload capacity flight: military UAVs.
2. DEFINE |
To establish a competitive advantage in the agricultural drone market, we defined the following key performance requirements:
Payload Capacity: 90 kg
Endurance: 4 hours of continuous operation before refueling or recharging
Structural Efficiency: Optimized for minimal weight with a high lift-to-weight ratio
Durability: Engineered to withstand harsh environmental conditions
3. DESIGN |
Hybrid Power
Inspired by UAVs and other high-payload aircraft, we decided to integrate jet engine propulsion into our design. By leveraging a hybrid power system—combining fuel and battery power—we aimed to enhance performance and extend the operational lifespan of battery-powered drones. The jet engines would provide intermittent thrust for propulsion, while battery power would be used for precise directional control. Furthermore, we optimized the drone's aerodynamics to maximize glide efficiency, allowing for extended unpowered flight following propulsion activation.
By performing airfoil optimization analysis on our constraints, we landed on a fixed delta wing with a high-aspect ratio and anhedral (downward) wing-tips to increase maneuverability.
We selected durable lightweight materials for the construction, including aluminum for the frame, a lightweight molded composite for the body, and a carbon fiber shell.
Engine Optimization
By modifying combustion chamber intake geometry, we could improve catalytic conversion efficiency and prevent air backflow.
We could leverage the Coanda effect to improve compressor intake, and increase the stagnation efficiency of the centrifugal compressor.
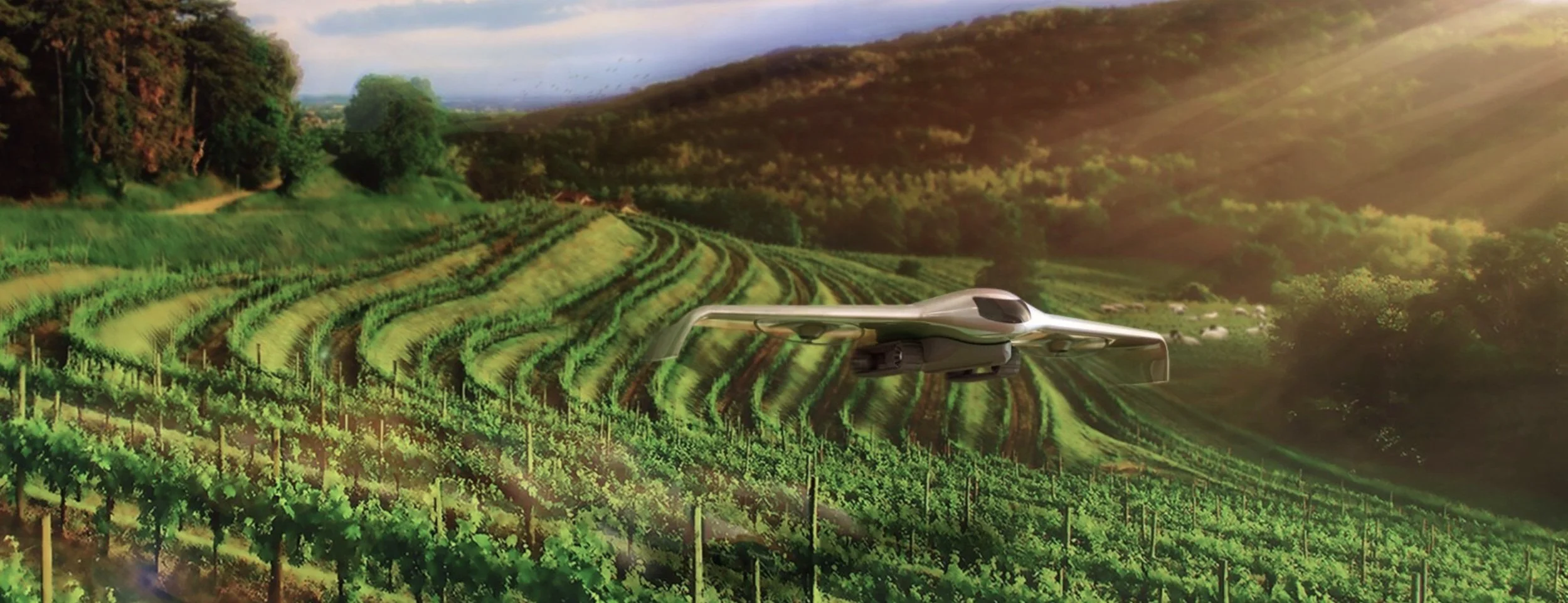
4. PROTOTYPE |
We partnered with a local advanced manufacturing prototype shop to produce additive metal manufacturing and CNC machining to produce rapid turn-around models for the combustion chamber and compressor prototypes.
For the body of the drone, we used aluminum for the structural frame, and cut cross sections of high density foam to produce the tapered air foil. We manually wrapped the body using carbon fiber sheets and epoxy.
5. TEST & ANALYZE |
Using a small-scale RC jet engine, we modified the internal geometry by inserting our prototype engine elements and measuring the output thrust. We found that compared to baseline thrust, we were achieving ~4% increased thrust efficiency with our initial iterations.